Introduction: Safety Culture in Factories
Creating a robust safety culture in factories is not merely a regulatory requirement; it is a cornerstone of operational excellence and employee well-being. In the dynamic industrial landscape of today, where the risks of accidents loom large, prioritizing safety is essential for minimizing workplace incidents, enhancing productivity, and fostering a positive work environment. This article will delve deeply into effective strategies for establishing and nurturing a safety culture within factories, ensuring that safety becomes an integral value embraced by all employees.
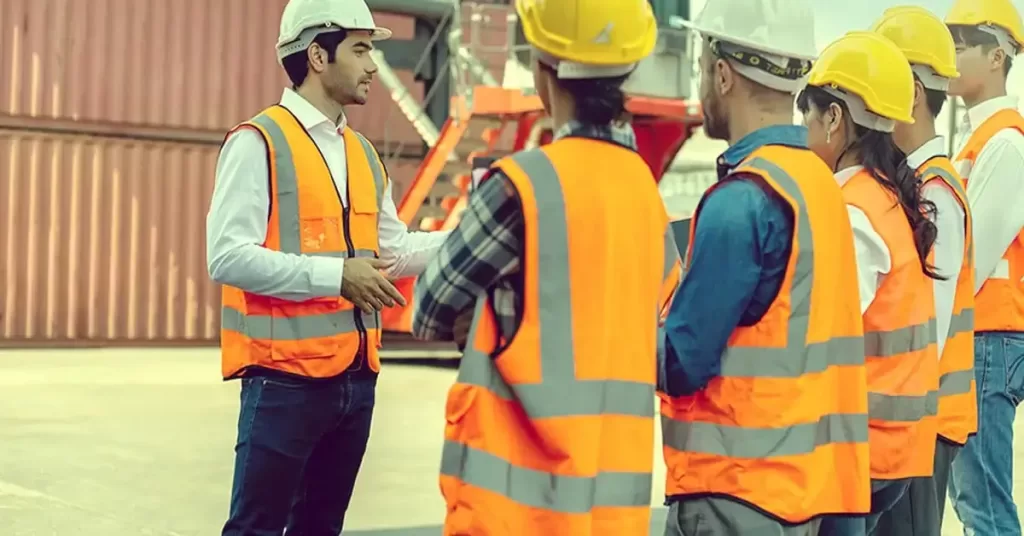
Understanding Safety Culture in Factories
Safety culture refers to the shared beliefs, practices, and attitudes regarding safety within an organization. In factories, where hazards are commonplace, cultivating a strong safety culture is imperative. This culture promotes active participation in safety protocols, encourages hazard recognition, and fosters a proactive approach to risk management. Research indicates that organizations with a well-established safety culture experience fewer accidents and injuries, leading to improved operational efficiency and reduced costs.
1. Leadership Commitment: The Foundation of Safety Culture
The commitment of leadership is crucial for a safety culture to thrive. Leaders must not only endorse safety initiatives but also embody safe behaviors. This involves active participation in safety training sessions, conducting routine safety audits, and being visibly involved in safety meetings. A study published in the Journal of Safety Research reveals that visible leadership commitment correlates with lower incident rates and heightened employee engagement in safety practices.
2. Open Communication: Encouraging Dialogue on Safety
Open communication channels regarding safety are vital. Employees should feel empowered to report unsafe conditions or behaviors without fear of retaliation. Establishing safety committees or forums for discussing safety concerns fosters trust and collaboration. Regular safety meetings, both formal and informal, can provide platforms for these discussions, allowing employees to voice their opinions and share experiences. According to a report by the National Safety Council (NSC), organizations that encourage open dialogue about safety see a significant reduction in workplace accidents.
3. Comprehensive Training Programs: Equipping Employees with Knowledge
Training is a cornerstone of building a safety culture. Factories should implement comprehensive safety training programs covering all aspects of workplace safety, including proper equipment usage, emergency procedures, and hazard recognition. New employees should undergo rigorous onboarding training, while existing staff should participate in ongoing training sessions to keep their knowledge current. Incorporating hands-on training and simulations can enhance learning and retention. The Occupational Safety and Health Administration (OSHA) emphasizes that regular training is a key factor in reducing workplace injuries.
4. Empowering Employees: Ownership of Safety Practices
Empowerment is fundamental in fostering a proactive safety culture. Encourage employees to take ownership of safety practices by involving them in safety audits, risk assessments, and the development of safety protocols. By giving employees a voice in safety matters, they become more invested in creating a safe working environment. Recognition programs that celebrate employees who demonstrate outstanding safety practices further enhance this ownership. Research from the American Society of Safety Professionals shows that companies with empowered employees report higher safety compliance and lower accident rates.
5. Continuous Improvement: Adapting to Evolving Safety Needs
A safety culture is not a static initiative; it requires ongoing development. Factories must regularly review and update their safety policies and practices to adapt to changing conditions and technologies. This involves analyzing accident reports, conducting safety audits, and seeking employee feedback to identify areas for improvement. By fostering a culture of continuous improvement, factories can proactively address potential hazards and ensure a safer workplace. The International Journal of Industrial Ergonomics underscores the importance of continuous feedback loops in maintaining a strong safety culture.
6. Utilizing Technology: Enhancing Safety Measures
Incorporating technology into safety practices can significantly enhance a factory’s safety culture. From wearable safety devices that monitor employee health and environmental conditions to software that tracks safety training and incident reports, technology provides valuable insights into safety performance. Additionally, implementing automated safety systems can help reduce human error, a leading cause of accidents in factories. The integration of technology not only streamlines safety processes but also empowers employees to take a more active role in safety monitoring.
7. Recognizing and Rewarding Safe Practices
Acknowledging and rewarding safe behaviors is crucial in reinforcing a safety culture. Factories should establish recognition programs that celebrate individuals or teams demonstrating exceptional commitment to safety. This could take the form of awards, bonuses, or public acknowledgment in safety meetings. Such incentives encourage employees to prioritize safety and inspire others to follow suit. Research from the National Safety Council indicates that recognition programs can lead to a significant increase in employee engagement and safety compliance.
8. Creating a Safe Work Environment: The Physical Space
A significant aspect of safety culture is the physical work environment. Factories should ensure that workspaces are designed with safety in mind, including adequate lighting, ventilation, and ergonomic layouts. Regular maintenance of machinery and equipment is crucial to preventing malfunctions that could lead to accidents. A well-maintained and organized workspace reduces the risk of injuries and promotes a culture of safety. The Journal of Occupational Health Psychology states that a well-designed workplace can significantly reduce workplace stress and improve overall safety.
Timeline of Safety Culture Development in Factories
- Year 1 (2024): Leadership commitment established; initial training programs implemented.
- Year 2 (2025): Open communication channels created; safety committees formed; initial accident rate analysis conducted.
- Year 3 (2026): Comprehensive training programs expanded; technology integration begins; employee feedback mechanisms implemented.
- Year 4 (2027): Empowerment initiatives rolled out; continuous improvement processes evaluated; recognition programs launched.
- Year 5 (2028): Workplace safety metrics show significant improvement; regular safety audits and updates become routine.
Expert Opinions on Building a Safety Culture
Dr. Sarah Thompson, a workplace safety expert with over 15 years of experience, emphasizes, “Creating a safety culture is not just about compliance; it’s about embedding safety into the core values of the organization. When employees feel responsible for their own safety and that of their colleagues, they actively contribute to a safer work environment.”
John Stevens, a safety consultant who has worked with numerous manufacturing firms, adds, “Effective communication is the backbone of a safety culture. When employees can freely share their concerns without fear, it creates a proactive approach to safety rather than a reactive one. This not only improves safety metrics but also enhances employee morale.”
Conclusion: A Commitment to Safety is a Commitment to Success
In conclusion, building a safety culture in factories is a multifaceted process that requires commitment, communication, training, empowerment, and continuous improvement. By prioritizing safety and creating an environment where employees feel valued and involved, factories can significantly reduce accidents and injuries. Ultimately, a strong safety culture protects employees and enhances productivity and contributes to the overall success of the organization. Adopting these strategies will lead to a safer, healthier, and more productive workplace for everyone involved.
📚 Take Your Trading And Financial Skills to the Next Level!
If you enjoyed this post, dive deeper with our Profitable Trader Series—a step-by-step guide to mastering the stock market.
- Stock Market 101: Profits with Candlesticks
- Stock Market 201: Profits with Chart Patterns
- Stock Market 301: Advanced Trade Sheets
Start your journey now!
👉 Explore the Series Here
For Regular News and Updates Follow – Sentinel eGazette
FAQs
Q1: What is a safety culture in factories?
A safety culture in factories refers to the shared values, beliefs, and practices regarding safety among all employees. It promotes proactive safety measures and encourages employees to recognize and report hazards.
Q2: How can leadership influence safety culture?
Leadership plays a crucial role by demonstrating a commitment to safety, participating in training, and fostering open communication about safety concerns, thereby setting a standard for the entire organization.
Q3: What are the benefits of a strong safety culture?
A strong safety culture can lead to reduced accident rates, increased employee morale, enhanced productivity, and lower insurance costs, creating a safer and more efficient workplace.
Q4: How often should safety training be conducted?
Safety training should be conducted regularly, including comprehensive onboarding for new employees and ongoing sessions for existing staff to keep safety practices updated and relevant.
Q5: What role does technology play in enhancing safety in factories?
Technology can enhance safety through tools like wearable devices for monitoring health and environmental conditions, software for tracking safety compliance, and automated systems to reduce human error.